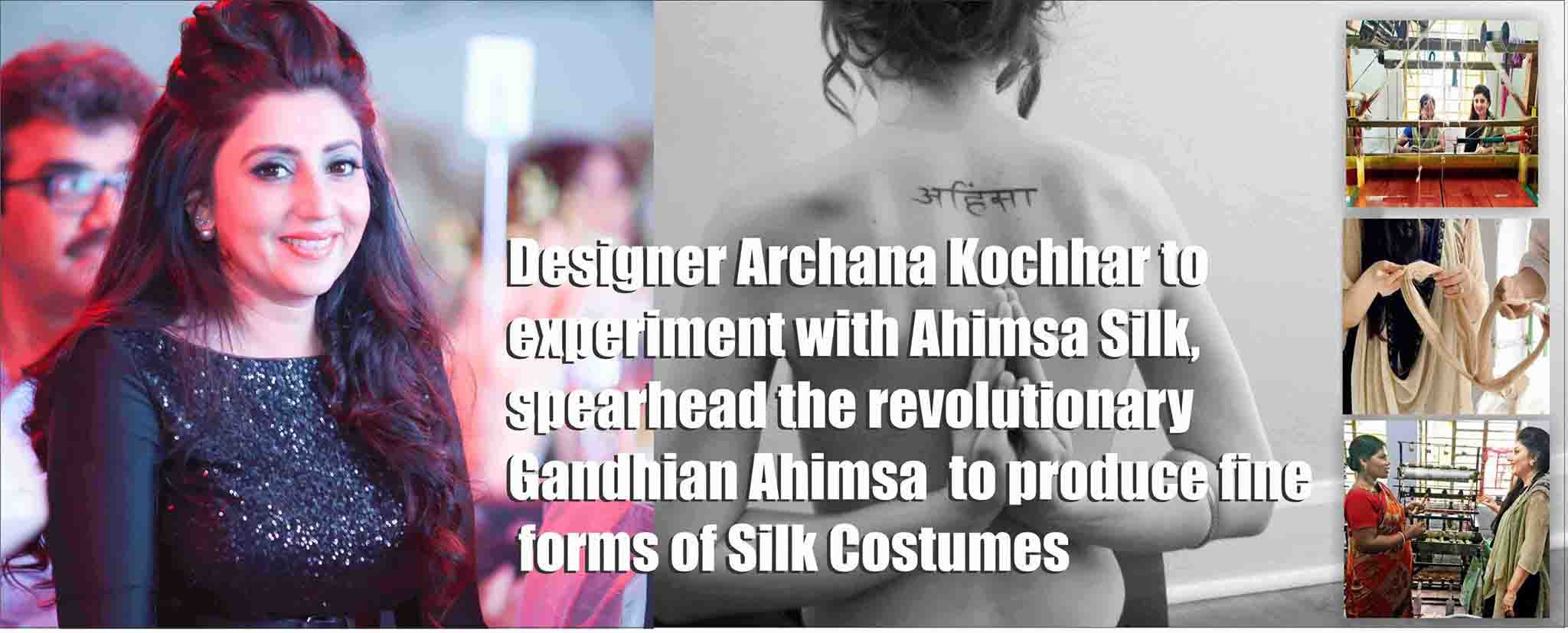
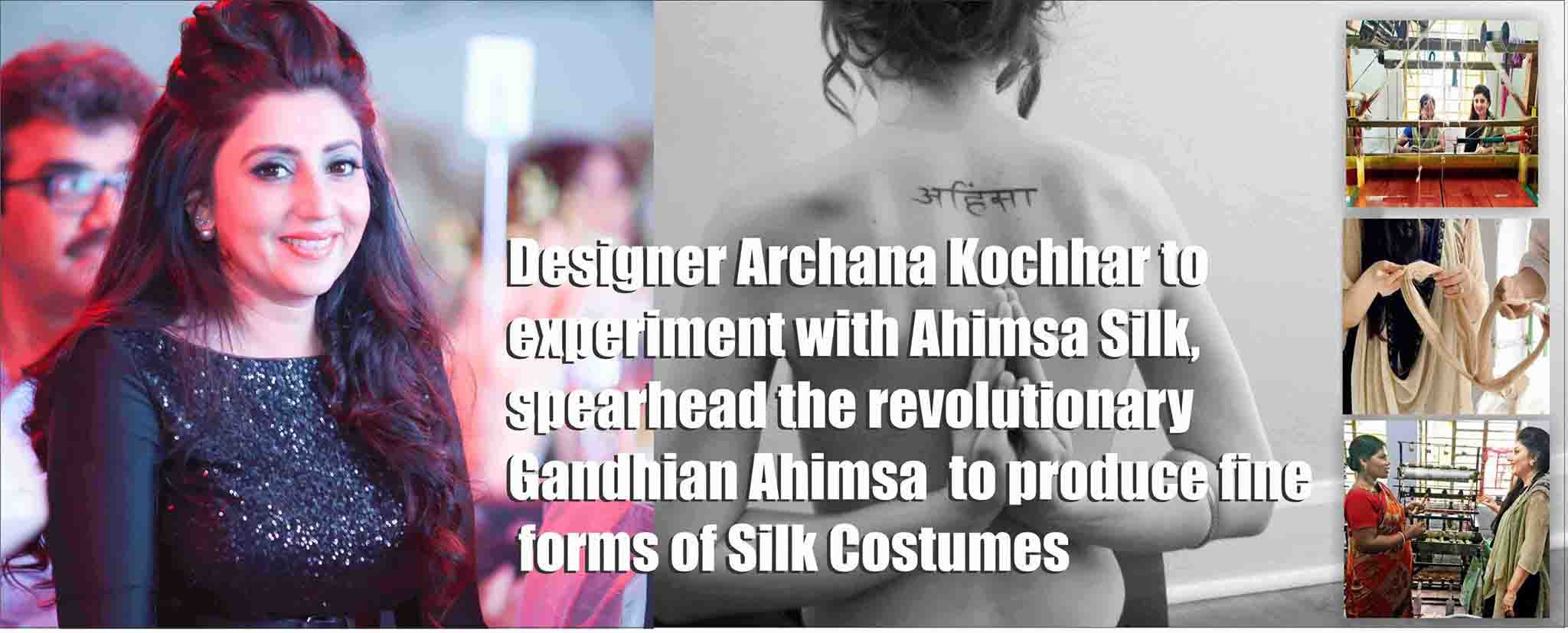
Designer Archana Kochhar to experiment with Ahimsa Silk, spearhead the revolutionary Gandhian Ahimsa to produce fine forms of Silk Costumes
Organic nature, extraction technology, handwoven coupled with Indian Government’s support to Celebrity Designer Archana Kochhar prompted her to find an increase in Livelihood for Women Weaving Community
Unfortunately in india we have a tendency to forget an age old tradition as we embark newer ways of innovation & presentations, Indian weaving industry which constitute a sizeable working force today is fighting for its better livelihood & better standard of living. Impressed by the visit to Jharkhand & working with the women weaving community, Archana decided to give a major boost to Ahimsa Silk which had lost its relevance economically as well as culturally. Archanna realized that the weaving community which are geeting Rs 5000 Per Month despite putting their hard work can actually earn 8000 to 9000 Rs per month given its potential & appeal. In India, this concept is not new but it was not taken up in a big way as the technology to process the yarn and later weave it were not developed. Now, Fashion designer Archana Kochhar has collaborated with Jharkhand Silk Textile and Handicraft Development Corporation to promote ahimsa silk for her next collection. Kochhar is currently working on a collection that uses this silk, and will be participating in the Mercedez Benz New York Fashion Week in September.
@Archana_Kochhar to experiment with Ahimsa Silk, Gandhian Ahimsa @ShraddhaKapoor @SunnyLeone pic.twitter.com/kE4X40yUZu
— Indian Affairs (@Indian_Affairs) September 7, 2015
The production of ahimsa silks involves waiting for the caterpillars to finish the cycle and leave the cocoon as a moth. Each cocoon is checked individually to ensure that the moth has escaped before the silk thread is spun. Kochhar tells us that though this process produces 60% of amount of silk as compared to the regular method, it meets the purpose of fashion for a cause.
We have seen many protests worldwide against the use of leather products. However, surprisingly, there hasn’t been much resistance against the use of silk garments, especially considering the fact that thousands of silkworms are killed in order to make a small piece of fabric. Silk comes from the cocoons of the silk worm (bombyx mori). In the silk industry, cocoons are killed by steaming or dropping them into boiling water when they are ten days old, before they metamorphose into a moth.
The silk is believed to be the finest at this stage. This is preferred because when the cocoons open naturally at one end, to release the moth, the continuity of the fibre is lost. The pierced cocoons are spun into yarn. This is then woven into fabrics.
The Background
Kusuma Rajaiah, an Indian man, has developed a new technique for producing silk that does not require killing silk worms in the process. [Note: We’ve been informed that a company in Oregon, Peace Silk, already uses this technique]. Right now, producing a silk saree involves killing of at least 50 thousand silkworms. Rajaiah has won the patent for producing the “Ahimsa” silk. Ahimsa is a religious concept which advocates non-violence and a respect for all life. However, the production of the silk is more expensive. For example, a saree which costs 2400 rupees to produce using regular silk, will cost 4000 rupees when made with Ahimsa silk.
Rajaiah says: “My inspiration is Mahatma. He gave a message to the Indian silk industry that if silk can be produced without killing silkworms, it would be better. He dreamt but that did not happen in his lifetime. I am the happiest person that at least I could do this little thing.”
Rajaiah says he started giving a serious thought to “Ahimsa” silk when in the 1990s. Janaki Venkatraman, wife of the former President, asked if she could get a silk saree that is made without killing silk worms. Yarn for a silk saree is usually produced by throwing live cocoons of silkworm into boiling water. A single saree needs upto 50,000 cocoons. Rajaiah allows the moth to escape from the cocoon by waiting for 7-10 days and then uses the shells to produce yarn. One’s clothing can be as Spartan as Gandhiji’s attire of a white homespun cloth wrapped around oneself or as thoughtlessly insensitive as silk clothes and leather jackets. From khadi to silk, one travels the entire range of clothing representing stark utilitarianism at one end and cruelty-based vanity at the other.
For most Indian women the use of silk has become a status symbol. Soft, smooth and shimmering silk is perhaps the most attractive textile man has ever created. More than two thousand years ago, this fabric was imported from China, hence in Sanskrit it was known as Chinanshuk. The method and source of its production was a very highly guarded secret; may be because it involved the killing of millions of lives.
Annually 155,000 metric tons silk is produced worldwide. Of this China, the largest producer of silk produces 65,000 metric tons, whereas India at second place produces about 23,060 tonnes a year which generates a turnover of Rs 25,000 crore of which Rs 2,500 crore is exported. (70 lakh people are involved: 5 lakh are sericulture farmers and the rest are other stakeholders such as reelers, twisters, weavers, printers, etc.) Other silk producing countries are Brazil, Korea, Japan and Vietnam.
Countries which import Indian silk are USA, UK, UAE, Italy, Spain, France, Germany, Saudi Arabia, Afghanistan, China and some others, but export has declined due to US buyers procuring the material from other markets like China. Nevertheless, huge quantities of silk waste get exported.
In order to safeguard the interests of the Indian silk industry, in 2009 India renewed for 4 years the anti-dumping duty on Chinese raw silk imposed in 2003, and till 2011 on fabric which had been imposed in 2006. However, due to demand being more than the India supply, the duty did not stop China from exporting raw silk to India and the price of raw silk rose. By the end of the 11th Plan, the Government set a target for silk production of 26,000 tonne and an export turnover of Rs 4,500 crores, but luckily even by 2013 India was yet to achieve it.
In 2013 Government increased the 12th Plan target to 32,000 tonnes of raw silk which included 5,000 tonnes of superior quality bivoltine raw silk. Also an additional 59,000 hectares was proposed for growing mulberry.
In 2003 the Central Silk Board began introducing Tussar silk production to tribals in regions such asBanka and Jamui districts of Bihar. Their projects covered entire support from nurseries to spinning technology.
In 2012 The National Bank for Agriculture & Rural Development (NABARD) proudly declared having given working capital support to a Tussar silk reeling unit owned by tribal women in Bihar. This was followed in 2013 by a state-level initiative covering 17,500 beneficiaries.
In 2013 the International Sericultural Commission (a global inter-governmental body set up in the 1960s) moved its headquarters from France to India. Unfortunately this gave India more access to genetic resources for increasing silk production and ending the supply-demand gap of around 5,000 tonnes. (Supply had risen to around 26,000 as had the demand to 36,000 tonnes.)
BWC was pleased that production and exports of silk was lessening in 2013 when MGNREGA (Mahatma Gandhi National Rural Employment Guarantee Act) which provides at least 100 days of paid annual employment in rural areas was extended to sericulture by the government. India’s silk exports had fallen to $155 million in FY2013. (Exports had touched $380 million in FY2008, and earlier were $238 million in FY2000, while exports of silk carpets had risen to as much as $945 million.) Meanwhile China maintained its 80% global share selling silk 20-30% cheaper than India whose global market share was 17.5%.
The Making of Silk
Silk worms survive in the range of 22 to 28 degrees Celsius. Therefore, in different parts of India they are reared and harvested 2 to 5 times a year. (Mulberry takes around 25 days and eri up to 18 days.)
The filament of silk is what a silkworm spins its cocoon of and is constructed as a shell to protect itself during its cycle of growth from caterpillar to chrysalis to moth.
The female moth lays about four to six hundred eggs. The eggs hatch in about ten days and the larvae (one-twelfth of an inch in length) emerge. They are fed on mulberry leaves for about twenty to twenty-seven days, till they are fully grown (three to three and a half inches in length). A fully grown caterpillar emits a gummy substance from its mouth and wraps itself in layers of this filament to form a cocoon in two to four days. The caterpillar develops into a moth in about fifteen days. To emerge it has to cut through the cocoon — thereby ruining the filament of the cocoon.
Hence, to save the filament from being damaged, the chrysalis is either immersed in boiling water, passed through hot air or exposed to the scorching heat of the sun’s rays, thus killing the lives inside. The long, continuous filament of the cocoon is then reeled. To produce one hundred grams of pure silk, approximately fifteen hundred chrysalises have to die. (Momme weight is the weight of a standard piece of silk fabric measuring 100 yards long and 45 inches wide.)
Particular chrysalises are kept aside to allow the moths to emerge and mate. After the female moth lays eggs, she is always mercilessly crushed to check for diseases. If she appears diseased, the eggs laid by her are immediately destroyed.
Generation after generation of inbreeding has taken away the moths’ capacity to fly – the most they can do is jump. After mating, the male moths are dumped into a basket and thrown out. It is a common sight to see crows picking at them outside silk manufacturing centres.
Cruel, not Eco-friendly
It was shocking to learn, scientists from the National Chemical Laboratory, and Central Sericultural Research and Training Institute added azo dyes to the silkworms’ leafy diet so that they would spin coloured silk and it would not require dyeing. It is cruel, not eco-friendly as claimed… dye is sprayed on the leaves to modify them which is harmful for the environment and the worms who consume them. The dye passes through the digestive canal of the silkworms and enters the silk glands so the cocoons obtained are a lighter shade of the coloured dye used. Calling the resultant silk bio-organic is a sales gimmick.
Varieties of Silk
The country’s largest cocoon market is in Ramanagram, near Bangalore. The Central Sericulture Research and Training Institute, Mysore, have with the help of Japanese experts developed the bivoltine variety of silkworms with which the farmers are being lured and the Central Silk Board (set up in 1948 by an Act of Parliament) has plans to promote them in other silk rearing States like Andhra Pradesh, West Bengal, Jammu & Kashmir, Uttar Pradesh and Tamil Nadu.
To boost export of cocoons from Maharashtra, the state government decided to increase production of bivoltine cocoons resulting in a 100% rise during 2009-10. The government buys 50% of the cocoons from the farmers.
60% of Indian silk is produced in Karnataka State. Other major silk producing states are Tamil Nadu (with output of 1,400 tons), Andhra Pradesh, West Bengal and J&K. Export earnings are to the tune of Rs 2,500 crores per annum.
Interestingly, a July 2010 report about Karnataka says that the state’s 60% share of the country’s silk production has fallen to 37%. According to statistics available with the CSB, mulberry acreage in the state stood at 1.66 lakh hectare in 1998-99 before Bangalore witnessed the IT boom. It declined by half to 0.88 lakh hectare in 2002-03 and further to 0.77 lakh hectare in 2008-09. There is huge real estate development in the area and around 30,000 agricultural families involved with mulberry cultivation have left to seek other streams of revenue.
Mulberry leaves is the only silkworm food plant and till March 2011, S-146 was the only popular mulberry genotype for silkworm rearing. So in order to increase silk production and reduce importing from China, (and other countries like Uzbekistan, Korea, Japan and Thailand) the CSB authorised three mulberry varieties for commercial use by sericulture farmers in India: Victory-1 (V-1), Anantha and Vishala. Sericulture Research and Training Institute, Sericultural Research Station in Andhra Pradesh and Karnataka State Sericultural Research and Development Institute in Bangalore are breeders of these three mulberry varieties. While V-1 and Anantha were recommended for commercial use in Karnataka, AP and TN, Vishala was authorised for all sericulture regions in India.
With the object of getting into the Guinness Book of World Records, the world’s lightest silk gold zarisaree (6 metres x 44 inches, weighing 70 grams from fibres of 3 to 4 cocoons) and a scarf (1 square metre weighing 30 grams from fibres of 2 cocoons) was woven by a Karnataka silk farmer and presented to the US President Barack Obama in 2010. With this it was also hoped that export to the USA would increase – in any case USA is the top importer of Indian silk. Then, in 2015 kimkhwāb/hiranyamaterial hand-woven in Kashi was presented to the US First Lady, Michelle Obama. Thiskimkhwāb/hiranya was silk gold zari woven into heavy brocade. Till the 19th Century this material was almost always woven entirely from fine gold or silver threads and some times set with precious stones.
India is the only country that commercially produces all four varieties of silk obtained from four types of moths. These are known as Mulberry, Tussar, Eri and Muga. Mulberry is also produced in other silk producing countries like China, Japan, Russia, Italy, South Korea etc., but Eri and Muga are produced only in India. The Tussar silk is often produced by the caterpillar of a wild silk moth that is found in rain forests of Bihar, Jharkhand, Orissa, Chhatisgarh, Madhya Pradesh, Andhra Pradesh and Maharahstra. Unlike mulberry silkworms, these caterpillars are difficult to cultivate in captivity, so the cocoons are some times gathered from the wilds. However, it is not commercially viable to collect Tussar silk cocoons from jungles. Jungle Ghicha silk and Kosa silk (mainly produced in Chattisgarh from a worm similar to silk worm) are sales gimmicks. Ghicha or Khewa are the names given to yarns that are not dyed when Tussar silk is reeled.
The Central Silk Board which is the apex body of the Indian silk industry promotes silk in different ways and is proud to have increased production of Eri spun silk. Eri silk is produced in Assam, Bihar, West Bengal and Orissa. Certain tribes of North East India eat Eri silkworm pupae. And, as these pupae are high in oil content pupal oil is extracted from them for use for making cosmetics. The remnants called pupal cake is fed to poultry and fish. Silkworm litter (read killed moths and destroyed eggs) is used as fuel for cooking in rural areas and more recently for bio-gas production.
Tamil Nadu, Karnataka and Andhra Pradesh together produce 80% of India’s total silk. This silk is all Mulberry silk. At Kanchipuram (famous for sarees of that name) weavers and looms are drastically lessening. Nearby Arani has overtaken production of these sarees although the dyed silk yarn is still procured from Kachipuram where the water from the river Palar is said to impart a unique shine to the silk.
In 2010 the government decided to include sericulture and allied activities in the Rashtriya Krishi Vikas Yojana of the XI Plan to make them eligible for funding under the scheme.
However, the good news is that people are opting for synthetic and embroidery sarees over traditionalIkat tie and dye sarees which they wear on special occasions. For example, the market for Andhra Pradesh handwoven silk sarees like the Pochampaly silk has over the last 7-8 years come down by 40%.
Man-made materials that look some what like silk are known as Artificial Silk (Art Silk). Of these, rayon (viscose) is of vegetable origin, whereas nylon and polyester (terrene) are petroleum products. Acetate/natural acetate filament that has begun to be widely utilised is cellulose derived fibre/yarn made from wood pulp. The filament is used in broad and luxurious range of silk (and woollen) fabrics.
Surprisingly, in October 2011 the international luxury brand Hermès, branching out on the popularity of their silk scarves (some having Indian designs) marketed in India a limited edition of French-made silk sarees. Hermès collectable silk ties they say are their biggest strength.
These could be Pure Silk:
- chania-cholis and gharcholas
• kameez and churidars/salwars
• chunnis/duppatasand odhanis
• sarees, petticoats and blouses
• pooja clothes (like dhoti and kurta)
• kafnis, soorvals, sherwanis
• telia rumals(as lungis, shoulder-cloths and turbans)
• mojadis (open shoes)
• skirts and dresses
• suits, jackets and coats
• shirts
• dance costumes
• ties
• nightwear and underwear
• handkerchiefs and stoles
• stockings, scarves and gloves
• headgear such as caps and hats
• ribbons
• handbags
• curtains
• upholstery
• lampshades
• carpets and wall-hangings
• lining and trimming for various clothes
• typewriter and printer ribbons
• cords with tassels on traditionally designed
• gift envelopes
• embroidery thread and embroidered items
• thread used for surgical sutures
• thread used for stringing beads like rudraksha and pearls
The Silk content of some Materials
Once woven, silk is known by different names depending on the weave, style, design and place where it is woven. In the following selections, are put together the most well known materials according to their silk content.
Zari (gold, silver or copper brocade yarn or thread) is traditionally used to embellish sarees and materials and is woven into the fabric, embroidered or used as patchwork. Zari is used for Kamdani, Mina, Kataoki Bel, Makaish, Tilla/Marori, Gota and Kinari embroidery work. Commonly known Zardoziwork is embroidery usually on heavy silk, velvet or satin with zari of different thicknesses having embellishments like beads and seed pearls. Since 2009 Varanasi zardozi weavers have been losing foreign orders (e.g. for monograms and badges for the Army in UK) because such work is supplied by Pakistani artisans for 25% less. In 2013 Lucknow zardozi got the Geographical Indication (GI) label or tag.
There are three types of zari: real, imitation (in recent times known as “tested” zari) and plastic. Realzari is a flat silver wire which has been electroplated with gold. Immitation/tested zari is made from copper wire electroplated with silver and then gold plated. Plastic zari is produced from chemically-coloured metallic yarn. Zari wire is wrapped around silk/polyester yarn and electroplated with gold for pure zari and with chemicals in case of artificial zari. However, caution needs to be taken with regard tozari because the yarn used for this can be silk or polyester. For real/pure gold zari, silk yarn is almost always used.
In Surat alone every month around 1,500 kgs of basin silk procured from Sidlaghatta in Karnataka is utilised for making zari. Varanasi is another main production centre for zari in India. Melted metal bars are beaten to particular lengths and pulled through perforated steel plates to form wires which are thinned down with rubber and diamond dies. Badla is the final process in which the wires are flattened and twisted along with silk or cotton yarn to become kasab or kalabattu threads which forms the zari. Depending on thickness and type, the zari is used for weaving, embroidery, tassels or as drawstrings for purses and necklaces.
The standard specification for real zari is 24% silk, 55-57% silver and 0.6% gold. (Due to rising prices the Tamil Nadu government in 2012 allowed zari of Kancheepuram silk sarees – protected by the GI tag – to have 40% silver and 0.5% gold, i.e. 50 grams of silver plated with gold; but most weavers have switched to using tested zari. Incidentally, Bhagalpur silk of Bihar also has the GI tag.) Plastic zari (very much cheaper than imitation/tested zari of copper) is made of alternatives like polyester film coated with aluminium but that does not necessarily mean the yarn utilised would also be polyester and not silk.
Lurex (brand name) is a type of yarn or thread with a metallic appearance used mainly for knitting and weaving. The twine is usually a synthetic fibre onto which an aluminium layer has been vaporised.
In 2012 the Central Silk Board decided to develop toughened silk material for jeans. The fibre required for two silk sarees will be needed for one pair of trousers. This was because the silk industry was growing at only 5% due to women wearing sarees occasionally.
100% Silk Materials
• Boski
• Charmeuse (crepe or satin woven)
• Chinese silk (can mistakenly be called China silk)
• Crepe de Chine
• Doupion (Italian and Chinese)
• Ghicha silk
• Habotai silk
• Khadi silk
• Kosa silk
• Muga silk
• Noil
• Pure chiffon
• Pure crepe
• Pure gaji
• Pure georgette
• Pure/silk satin
• Raw silk
• Silk brocade
• Silk jacquard
• Silk organza
• Silk shantung
• Spun silk
• Silk taffeta
• Tussar silk
• Matka silk is also 100% pure silk. In this, the yarn in warp is the usual silk yarn, whereas the yarn in weft is obtained from the cocoons that are cut open by the moths as they emerge. Later after they have laid eggs, these moths are crushed to death. Recently with a view of selling this silk under false pretences of it being ahinsak or involving no killing, it is being marketed as Endi silk.
100% Silk Sarees
• Baluchari
• Banarasi (Varanasi)
• Bangalore
• Bhagalpur
• Conjeevaram
• Dhakai
• Dharmavaram (boasts of being the silk city of India)
• Endi
• Kanchi/Kanchipuram/Kancheepuram
• Kanjeevaram
• Kashmiri
• Khambhat
• Matka
• Murshidabad (batik)
• Paithani (of Maharashtra – original handloom)
• Patola (of Patan, Hyderabad and Orissa)
• Pochampaly (of Andhra Pradesh)
• Semi-Paithani (of Maharashtra – powerloom)
• Silk felt/fusion
• Tanchhoi
• Temple
• Tussar
• Vishnupur
100% Silk or 100% Cotton Sarees
• Calcutta
• Gadhwal
• Madurai
• Shantiniketan
- Uppada/Jamdani sarees (Andhra Pradesh)
• Irkal sarees from Narayan Peth (Andhra Pradesh) can be 100% silk or part silk and part cotton.
• Venkatgiri and Mangalagiri sarees may be in all cotton or part silk and part cotton yarn.Sarees having Silk yarn in Warp and Cotton yarn in Weft or part Cotton and part Silk are
• Chanderi (of Madhya Pradesh)
• Maheshwari Sarees (of Madhya Pradesh) - Mushru(of Gujarat)
• Puneri (of Pune)
• Tissue
• Venkatgiri
• Manipuri Kota and Munga Kota sarees have both silk and cotton yarn.Some Blended (from silk, cotton, hemp or wool) Sarees and Materials are
• Bandhini/Tie dyed
• Batik/block printed
• Bidri and other Embroideries
• Cashmere
• Chamki/Khadi/Tinsel printed - Himroo
• Ikat/Chitka
• Khariwork
• PashminaSilk Materials which can also be made from Man-made Fibres are
• Chiffon
• Chinon
• Crepe
• Gagi
• Georgette - Jacquard
- Jersey
- Raschel
- Sateen (cotton)
• Satin (microfibre)
• Tabby/Moiré/Watered silk
• Taffeta - Twill
• Velvet
• Cheaper quality of tanchhoi can contain silk yarn in warp and artificial yarn in weft.
• The Japanese and Indian materials known as China Silk (not Chinese Silk) is not pure silk but polyester.Many 100% polyester sarees also look like silk particularly if they are in traditional designs and deep colours like purple, green and magenta. The first polyester brocade (zari) saree in silky finish woven on handloom by weavers in Varanasi was the result of four years research by BWC. In spite of this know-how being available, due the reluctance on the part of weavers and insufficient public demand, the sarees are not commercially available. In fact, the annual All India Saree Weavers Festivals hold exhibitions to promote silk sarees at low prices.Handlooms
Handloom karigari(traditional art) is closely linked to silk, so we find handloom sarees and materials mainly woven in silk. And, in their enthusiasm to use Indian textiles, our fashion designers promote silk garments (like lehengas, sherwanis, angarakhasand gowns) woven in brocade, Bhagalpur, Khand, Ilkal, Kalamkari, Uppada/Jamdani, Khadi, etc.Although Handloom Week is held every year from April 7 to 14, throughout the year “Weaves” and others – even the Krishna Khadi Gramdhoyog Sanstan’s “Silk India Silk” – exhibitions in different cities, showcase handlooms from almost every state and different cities of India, consisting of items such as sarees, dress materials, stoles, dupattas and home furnishings. They can be pure silk, cotton or a mixture of both, in Khadi too:
- Batik, Chanderi, Maheshwari and Indore silks from Madhya Pradesh
• Bagru, Sanganeri, Bandhini, Kota and Dabufrom Rajasthan
• Patola, Ikat, Ajrakh and Kutch embroidery from Gujarat
• Sambalpuri, Bomkai and Bhubaneshwar from Orissa
• Baluchari and Kantha from West Bengal
• Banaras, Chikan and Jamdani from Uttar Pradesh
• Kanjeevaram, Chettinad, Coimbatore, Chennai and Madurai silks from Tamil Nadu
• Tussar, Bhagalpur and Chudidar silk from Bihar
• Kosa from Chattisgarh
• Karvati, Kosa, Paithani, Mumbai and Nagpur silks from Maharashtra
• Kalamkari, Gadwal, Venkatagiri, Dharmavaram, Pochampally, Mangalagiri, Uppada, Chirala, Hyderabad, Vijayawada, Vizag and Guntur from Andhra Pradesh
• Bangalore and Mysore silks from Karnataka
• Cochin, Trivandrum, Kottayam and Thrissur from Kerala
• Delhi silk - Chandigarh silk from Punjab
The GI label or tag that safeguards the genuineness of products like handlooms from particular regions, thus successfully promoting them, has been granted to the following and possibly others too:
Andhra Pradesh: Pochampalli Ikat, Gadwal sarees, Venkatagiri sarees, Narayanpet Handloom sarees, Dharmavaram handloom Pattu sarees & paavadas, Mangalagiri sarees & fabric
Assam: Muga silk
Bihar: Bhagalpur silk
Chhattisgarh: Champa silk sarees & fabric
Delhi: Chanderi fabric
Gujarat: Patan Patola
Karnataka: Molakalmuru sarees, Mysore silk
Kerala: Kasaragod sarees, Kuthampully sarees
Madhya Pradesh: Maheshwar sarees & fabric
Maharashtra: Paithani sarees & fabric
Orissa: Kotpad Handloom fabric, Khandua sarees & fabric, Gopalpur Tussar fabric, Dhalapathar Parda & fabric, Sambalpuri Bandha sarees & fabric, Bomkai saree & fabric, Habaspuri saree & fabric, Berhampur Patta (Phoda Kumbha) saree & joda
Rajasthan: Kota Doria
Tamil Nadu: Kancheepuram silk, Arani silk, Salem silk or Salem Venpattu
Uttar Pradesh: Banaras brocades & sarees (logo), Lucknow Zardozi
West Bengal: Shantipore sarees, Baluchari sarees, Dhaniakhali sarees
GI tagged materials can only be marked and sold under these names if manufactured in specified regions. If not, according to the Act, products manufactured else where and marked as such could attract a fine of up to Rs 2 lakhs and imprisonment up to 3 years or both.
Gramsampada is an annual week-long expo organised by NABARD (National Bank of Agriculture and Rural Development) since 2008. Its purpose is to showcase products made in Maharashtra so one finds silk sarees like Paithani from Yeola, Nashik, and Tussar silk from Bhandara; Ghongadi (desi blanket from wool of sheep) and other woollen items from Sangola, Sholapur; plus, handlooms woven by visually impaired artisans of Latur. It would be better if they would solely focus on providing market exposure for handicrafts without silk and wool like bamboo handicrafts from Amravati and Nagpur, and cashew products from Sindhudurg.
In 2011 Anakaputhur weavers entered the Limca Book of Records by making sarees using 25 different natural fibres such as banana, flax, sea grass, lemon grass and messa. Such fibres – not forgetting jute, bamboo, soya, pineapple and milk (yes, milk) – are quite often blended with cotton or silk on handloom. Handloom materials are expensive but attractive because they are considered eco-friendly – unfortunately not always animal-friendly.
In July 2012 an engineer from Tuticorin was granted a patent on his invention of a banana yarn separator machine. The banana plant has 15 layers – the outermost is used for garlands, but the other 14 can be used for silk production since the fibre matches silkworm silk in lustre and tenacity.
A Test to Determine a Material’s Silk Content
In 2004, the Central Silk Board (under the Ministry of Textiles) sponsored the Silk Mark Organisation of India which has been advising manufacturers producing 100% natural or pure silk fabrics in India to use this logo/label. It comprises of an artistic line-drawing of a silk moth below which the words SILK MARK appear. In 2013 the Government again unveiled a “SILK MARK INDIA” label for the global market in pure silk. However, as all silk items do not carry this logo since registration for its use if needed, those of us who wish to be certain whether or not a material contains silk, need to check it ourselves.
Remember, it is a totally wrong impression that if a material is cheap it has no pure silk in it. It is advisable to check oneself and not rely on the shopkeeper’s word. If you would like to know what yarn is used in a particular material, use the flame test in the following way: (As shopkeepers generally do not allow the silk test by burning to be performed on their premises, a few threads could be asked for and burnt at home.)
To identify silk, you must burn some yarn. It is very important that a few threads from the warp, a few from weft and the zari thread stripped off the metal are individually checked by burning. Since human hair also burns like silk, it would be easier to learn by burning some fallen hair! Hold a strand together between tweezers and burn it. Observe carefully how it burns. When it stops burning, a very tiny (pin-head size) ash ball will be left behind. Rub it between your fingers and smell the powdered ash. The smell of burnt hair, silk, wool and leather is identical and the slow way in which it burns forming an ash ball, will also be the same. If the fibre is cotton or rayon, it will quickly flare up in flames and will not form any ash ball nor will it smell like burnt hair. If the yarn tested is a petroleum product like nylon or polyester, it will burn forming a tiny, hard, glass-like bead.
Polyester Silky Brocade
The first polyester brocade/zari saree in silky finish woven on handloom by weavers in Varanasi was the result of four years’ research by BWC. Despite this know-how being available since 1998, due to the reluctance on the part of weavers and insufficient public demand, the sarees are not commercially available.
No such thing as Ahimsak Silk
Beauty Without Cruelty holds the trademark and copyright for the brand names Ahinsa and Ahimsa. Despite knowing this, unscrupulous persons and organisations have gone ahead and used the Ahimsa brand name or by adding the suffixes such as Peace for marketing a particular type of silk. They know it is false and unethical, but for them it is the money that matters, not the lives that are killed for making the silk, or BWC!
By-products of Silk Industry
In October 2014 the Government of India permitted export of dried silk worm pupae to the European Union. Waste pupae are used as animal feed. Silk oil/liquid and silk powder are used by the cosmetic industry in products for moisturising and conditioning the skin and hair, in styling mousses for hair, and in some face powders and eye shadows. They are also used in the making of certain soaps.
In a new venture, the bark from mulberry trees which are annually pruned is utilised for making so-called ‘eco-friendly paper’. The production and use of this paper adds value to mulberry plantations thereby indirectly supporting silk production.
Similarly in Jammu & Kashmir scientists have undertaken initial trials of tea extraction from mulberry leaves and are encouraging the setting up of more mulberry nurseries so that farmers can grow mulberry not only for silk production but for tea production too.
Fried or boiled silk worms are consumed as a winter snack in Meghalaya. Eri/era worms which produce Assam silk and are known in the Khasi-Jaintia Hills as Niang Ryndia from which the Ryndia shawls worn by men are made, are the particular variety that are eaten. They are sold by worm-vendors in Lewduh (Bara Bazaar), one of the biggest markets of the North East.
Silk painting can be on silk or through silk as in the case of poster/banner making (the kind which are put up in public places for cinema hoardings, political campaigns, and as advertisements) if made conventionally (and not printed on plastic/polythene which incidentally were banned during poll campaigns by the Election Commission in 1999) involve the use of old silk sarees as a silk screen and shellac to mask/block out parts of the design that are not to be printed during the process.
Silk is also used for filtering. For example, Silent Sam Vodka is filtered through silk.
The Choice
What do we do if our uniform involves compulsorily wearing say a silk saree, leather shoes or some thing else of animal origin? We should first muster support from like-minded colleagues, then speak to the management explaining our ethical stand and at the same time find and show a very good non-animal origin alternative. For all we know, the management may get impressed enough to introduce our suggested alternative in place of the animal product.
Religion vis-à-vis Silk
Because silk is made by killing insects, it is considered tainted and therefore not used for religious ceremonies. For example, the Zoroastrian religion says silk should not be used in rituals: silk is made from a worm which is considered khrafastar and therefore unsuitable for ritual purposes. If a fabric is to be used for religious purposes, it should be cotton.
In daily life too some religions forbid the use of silk. The Jain laity is not allowed to wear it or even sell it. In fact, the ashinsak religion requires its adherents to follow a strict vegetarian diet and not take up occupations that involve killing any lives which includes silk.
Islam considers wearing silk (and gold) haram for men, but not women.
Interestingly, to curtail the craze for silk in the 1st century BCE, the Roman Senate issued several edicts prohibiting the wearing of silk on moral (and economic) grounds.
Another Good Reason for not using Silk
A new dimension involving child labour for silk production has been unfolded: for generations, poor people of Kancheepuram have for a couple of thousand rupees mortgaged their 10-12 year old children to work for the silk industry. Yet in 2010, Kancheepuram silk sarees received protection through the GI tag.
According to a Human Rights Watch’s 85-page report following investigations in Tamil Nadu, Karnataka and Uttar Pradesh, at least 3.50 lakh children, some as young as 5 years old, toil in the silk industry. For 12 hours work 6 days a week, these “slaves” endure beatings, burns and verbal abuse because they are bonded labour and bound to their employers in exchange for a large loan given to their families – a loan they can never earn enough to repay. The report states “The Indian government knows about these children and has the mandate to free them. Instead, for reasons of apathy, caste bias and corruption, many government officials deny that they exist at all”.
Despite laws against child labour existing, 2014 data collected suggested that 4,600 children were working in Mumbai’s zari workshops for 13 hours a day mainly making bags. They were from Bihar, UP, Rajasthan and Bengal. (Leather goods manufacturers, bakeries and hotels also exploit them for a couple of hundred rupees a week.)
Also, it has been reported that it is a practice for contractors to fleece farmers in Jammu and Kashmir by purchasing silk cocoons at very low prices.
Clams Spiders, Hagfish and Silkworms further Exploited
Byssus cloth or sea silk is an old and rare fabric. Long silky filaments (“beards”) secreted by a metre long pen shells or clams to attach themselves to the sea bed, are spun and treated with lemon juice. The silk produced is finer and lighter than silk form silkworms.
Spider silk was known as Nephila silk but it was found to be difficult to commercially produce. Hagfish, when captured escape by secreting a fibrous slime which includes threadlike fibres similar to spider silk so research to utilise these fibres is also being undertaken.
In 2000 Nexia, a Canadian biotech company began research to produce spider silk protein in transgenic goats. The goats carried the gene of spider silk protein and the milk produced by the goats contained significant quantities of the protein to produce Biosteel, however, Nexia is still continuing research for product development of Biosteel.
To make synthetic fibres and lightweight materials called hydrogels stronger and water-proof, researchers at Tufts University (USA) are trying to impregnate them with spider silk.
Producing spider-silk proteins in other organisms – goats, bacteria, plants and most recently silkworms are among those that have been genetically engineered – has limitations because the process of reconstituting the proteins ruins the folding pattern and simply said, it does not work. Therefore, researchers at Tuffs University think that eventually, genetically modified plants will produce useful spider-based silk that could be harvested like cotton. And the silk films developed from it could be used for implantable biosensors and in drug delivery.
However, since spider ranching is difficult and out of question, some scientists from the University of Illinois and University of Pennsylvania (USA) are working on reinventing silkworm silk. They have reconstituted it to make materials that have the potential to go far beyond the dream of bulletproof vests and have produced electrode arrays that are printed on flexible, degradable films of silk. The arrays – so thin they can conform to the nooks and crannies of the surface of the brain – they say, may one day be used to treat epilepsy or other conditions without producing the scarring that larger implanted electrodes do.
Also, Kraig Biocraft Laboratories has used research from the Universities of Wyoming and Notre Dame in a collaborative effort to create silkworms that are genetically altered to produce spider silk.
In 2012 a five year effort in Madagascar resulted in spider silk material measuring 11 x 4 feet which was fashioned into a cape and scarf and displayed at the Victoria and Albert Museum, London. The project cost $500,000 and involved 80 handlers who began collecting every day at 5 am as many as 3,000 female Golden Orb spiders and bringing them to the workshop at around 10 am. Incredibly, a total of 1,063,000 spiders were placed in hand-powered spools in groups of 24. As they manufactured silk, the filament was collected, twisted into strands, and finally woven into the golden textile. At 2 pm when the day’s work was over, the spiders would be reintroduced back into the wild. Poor spiders… the project is permanent.
Archana Kochhar’s Journey in Fashion Designing
Archana Kochhar is an internationally acclaimed Indian fashion designer with a creative approach to deal with the ever evolving fashion designing innovations blending a fine amalgamation of exquisite embroideries, nouveau texturizing techniques and new technologies like digital printing, all of this traditionally rooted. Going back to her initial days, Archana got into the world of Fashion way back in 15 years to make a foothold in Design, creative illustration of fine textile imprints using the state-of-art technologies like digital printing, fine arts & craftsmanship. Today, Archana is a much sought after name in Bollywood, Hollywood, bridal, cocktail prêt, resort and men’s wear. Archana’s fashion creativity & costumes are often seen in the high profile fashion shows, Red-Carpets & top event destinations. In an era where competition is intense & manifold where the demands for fine collections with a different look are sought after by the elite celebrities to cater, Archana has truly demonstrated & exhibited as a unique professional to redefine “Fashion Design” in the world. Archan’s flagship store located in the commercial capital of india in Mumbai, has reinvented itself over the years as a most trusted & reliable place to shop & try out different costumes. Creativity in Fashion design is about what you don’t see as well as what you do, the inside of a dress is as important as the outside. From the embroidery to the construction techniques, to the handwork that goes into them. Every single detail is thought about completely in Archna Kochhar’s fashion Library.
In the words of the gorgeous Fashion Designer Archana Kochhar, “fashion is an art that becomes artistic with each design. Subversive, creative design must remove itself from the standard, from what is known, and challenge society, while remaining recognizable enough that people can still understand and interpret it. So they can glean an experience from it. So it can stand as inspiration. It is this that imbues a fashion design with the potential to eventually become the new norm – the new standard. Creative subversion is necessary for the movement and evolution of society, not just in fashion, design and art, but for the development of social norms and the progression of intellectual thought. We are indebted to the creative, for without them we would be wallowing in the stagnation of popular, accepted thought, all modes the same and unchanging. Subversive creators play a role in our society, not as tastemakers, but as enlighteners. They challenge our minds and souls, the values we hold dear, our known interpretations of the world, of popular culture and the art and design that preceded it. They can both divide and unite people. They are simultaneously our history makers, our storytellers and our visionaries”.
Bollywood’s glitterati who have adorned her creations are some of the biggest names in Bollywood, Sports as well as modeling like Shraddha Kapoor, Sonakshi Sinha, Kangana Ranaut, Bipasha Basu, Karishma Kapoor, Chitrangada Singh, Urmila Matondkar, Nargis Fakhri, Jacqueline Fernandes, Prabhu Deva, Rajneesh Duggal, Vijender Singh, Randeep Hooda, Ileana D’cruz, Soha Ali Khan, Amrita Rao, Huma Quereshi, Daisy Shah, Celina Jaitley, Zarine Khan, Divya Khosla etc walking the red carpets and runways around the world.
Creativity can be an ecstasy of both pleasure and pain for the artist. Inspiration, when it strikes, is a powerful force that its recipient has little control over. The best fashion designers are held up by their industry as the veritable geniuses of our time. Whilst knowledge and training play one part in their creative passion and output, for centuries, theorists have wondered whether there are certain innate qualities that set artists apart, and put them in a unique position of creative ability.
Archana Kochhar’s care for the society is evident from the fact that as an Educationalist, Mentor & a guest Lecturer, Archana Kochhar is a visiting faculty to more than a dozen of colleges & is often seen in mainstream newspapers through her writing. Archana Kochhar has been invited by Galleries L’fayette Paris to showcase her spectacular collections under her label with international design houses like Armani, Versace, Kenzo, Ungro and Nina Ricci. She is a Goodwill Ambassador for Smile Foundation, working for the upliftment of the girl child and women empowerment. As a brand, Archana Kochhar is associated with many corporates due to her international design appeal and specialization in customizing each project that she curates ranging from interiors, jewelry, upholstery, weddings and fashion events with corporate giants like Reliance, Aditya Birla Group, Gitanjali, Sahara, Mahindra, to name a few. Over the years the brand Archana Kochhar has created a niche for itself and revolutionized the bridal arena with Archana Kochhar’s craftsmanship, detailing and expertise in her art. It has also made a mark globally and is well acclaimed not only in India but also in London, Dubai, Hong Kong, Bangkok, Canada and many other cities around the world. In Prime Minister Narendra Modi’s ‘Make in India’ campaign, few designers were chosen to revived the 5 dying arts , eminent Designer Archana Kochhar was one of them and she was bestowed by the Textile Ministry with the honor of being a brand ambassador for the revival of five dying arts of Maharashtra. Archana Kochhar was invited by the PARIS HAUTE COUTURE FASHION WEEK & the NEWYORK MERCEDES BENZ FASHION WEEK 2015 to showcase her collection in the international Fashion week Platform. Archana has been associated with SMILE foundation for Ramps for Champs & Cook for a Smile with Vikas Khanna. Exclusive designing of uniform for CLUB Mahindra. Lakme Fashion Week S/S 2014 had olympic silver medalist and Padmabhushan awardee Vijender Singh as showstopper. Jacqueline Fernandes launched Archana Kochhar’s summer/resort range in Dubai for Label 24. Chitrangada Singh & Urmila Matondkar launched Archana Kochhar’s Wedding range in Dubai. Nargis Fakhri walked for Archana Kochhar in the London Fashion Week Show in London. Kangana Ranaut walked for Archana Kochhar at the India Resort Fashion Week. Aditya Birla Group & Archana Kochhar launched and curated together the new viscose yarn with Soha Ali Khan. Archana Kochhar & Zarine Khan launch Gitanjali Jewels Nizaam range in Mimbai. Archana Kochhar launches her Chokhi collection at Lakme Fashion Week A/W 2013. Bipasha Basu walks for Archana Kochhar at Atlantis, Dubai. Shriya Saran walks the ramp for Archana Kochhar for the opening of India Jewellery week in Delhi. Prabhu Deva and Shahzahn Padamsee walked the ramp for Archana Kochhar for Lakme Fashion Week S/S 2013.Prime Minister Mr.Narendra Modi’s ‘MAKE IN INDIA’ campaign, few designers were chosen to revive some of the dying arts of India , eminent Designer Archana Kochhar was one of them and she was bestowed by the Textile Ministry with the honor of being a brand ambassador for the revival of five dying arts of Maharashtra. Designer Archana Kochhar is the Good Will ambassador of the organization “Smile Foundation” a charity cause for the Girl Child Health and Education in India. She believes in giving back to society and has helped in raising funds through her Charity events and shows for the Smile Foundation organization.
The beautiful Fashion Designer Archana Kochhar will be crowned as “Fashion Designer of the Decade” in a glittering award ceremony where some of India’s finest creative genius will be recognized in various categories. Rated by Experts & widely acclaimed by thought leaders, India Leadership Conclave Annual Affair is just not a leadership forum, it symbolizes the hopes & aspirations of the billion people reflected by the speakers at the forum. “ILC POWER BRANDS” has been rated in Asia as the most credible & coveted Awards developed by Network 7 Media Group consisting of eminent jury members of the different verticals of the society & is conferred to the Individuals & Companies in its annual meet at the Indian affairs India Leadership Conclave & Indian Affairs Business Leadership Awards. since the institutionalization of the Business Leadership Awards in 2010, India Leadership Conclave & Indian Affairs Business Leadership Awards has been India’s most awaited & asia’s most respected set of Awards conferred to Companies & Individuals who have made their mark through their remarkable performances despite all odds & has made India Proud!. Since the last five successful years, the platform has recognized, felicitated more than 300 fortune 500 Companies & towering captains & Leaders of the Country.